In the magical world of jewelry crafting, where intricate designs and exquisite materials make dreams come true, the advent of 3D printing has been nothing short of a revolution. Yet, for all its wondrous abilities, 3D printing occasionally meets its match in the face of certain materials and design complexities.
While these printers can create stunning and intricate designs with ease, there are limitations that artisans and designers must grapple with along the way. Some materials simply don't adapt well to the process. Others present challenges in geometry or lack the necessary strength post-printing. These hurdles force creators to find a balance between machine magic and human skill. Let's dive deeper into the world of unprintable elements in 3D printed jewelry to discover what still demands the touch of a traditional craftsman.
- Understanding 3D Printer Capabilities
- Material Limitations
- Complex Geometries and Details
- Durability and Strength Concerns
- The Role of Traditional Craftsmanship
- Future Prospects for 3D Printing
Understanding 3D Printer Capabilities
When diving into the potential of 3D printing, particularly in the realm of jewelry making, it's essential to first grasp what these technological marvels can accomplish. At its core, a 3D printer translates digital blueprints into tangible objects by meticulously layering material. This sublime interplay of science and creativity has unlocked a universe of possibilities, turning complex designs from ideas into reality.
The magic of 3D printing lies in its precision and customization. Jewelry designers can create pieces with intricate patterns that might have been impossible or incredibly labor-intensive using traditional methods. But there's a caveat—each 3D printer comes with its specific set of capabilities determined by the technology it employs. FDM (Fused Deposition Modeling), for instance, is great for basic prototypes but lacks the refined detail found in SLA (Stereolithography) or SLS (Selective Laser Sintering). Each method caters to different materials and levels of detail, thus impacting the final design's finesse and material choice.
A critical aspect not to be underestimated is the printer's resolution, which dictates the smoothness and intricacy of a piece. Resolution is typically measured in microns; the smaller the number, the finer the detail a 3D printer can achieve. While a resolution of 100 microns might suffice for larger or less detailed items, ornate jewelry often demands much finer gradations, dipping well below that threshold. A survey of jewelry designers using 3D printers found that a resolution of 25 microns or less was preferred for intricate styles.
Material versatility is another cornerstone of 3D printing's capabilities. The range spans from photopolymers to precious metals, each requiring a different process and offering unique strengths. For instance, while plastics like ABS and PLA offer affordability and accessibility, precious metals such as gold or silver are more costly and necessitate specialized machinery. However, it's crucial to remember that not every material is compatible with all printers. This diversity compels designers to be selective about the materials they choose, juggling between aesthetics and practical concerns like durability and strength post-printing.
Despite these advancements, traditional craftsmanship remains irreplaceable for those elements that can't be replicated by machine. "In crafting jewelry, the human touch still conquers machine precision in conveying soul and emotion," notes jewelry artisan Lenora Galls. This highlights the printer's supplemental role in the creative process rather than a wholesale replacement for traditional methods. No machine can yet replicate the warmth of human creativity fully. The future of jewelry design may very well rest on harmonizing these two worlds.
Material Limitations
When it comes to 3D printing in the realm of jewelry, one of the most significant challenges lies in the material limitations of the process. While 3D printing offers a myriad of possibilities, not every material plays nicely with the technology. Many people might dream of printing jewelry with precious metals like gold or platinum, but the realization of this dream is fraught with obstacles. Precious metals, known for their intrinsic value and luster, require extremely high temperatures for melting, which most standard 3D printers are simply not equipped to handle. Consequently, the ability to print directly with these metals is limited to specialized industrial-grade printers often inaccessible to individual artisans or small studios.
Moreover, the polymers typically associated with 3D printing, while proving versatile and fascinating, fail to replicate the strength and aesthetic appeal required for truly fine jewelry. They're perfect for prototyping or producing less costly end products, yet when it comes to creating pieces that need to endure the test of time and maintain a luxurious appearance, these materials fall short. The polymers might offer the versatility of complex shapes and lightweight designs, yet they miss out on the essential depth and intricacy of finer elements wrought by hand or in traditional metallurgy.
Interestingly, in the jewelry industry, even the introduction of resins and composite materials designed to mimic gemstones has only had partial success. While they can convincingly replicate the visual splendor of diamonds and sapphires from afar, these materials don’t possess the same refractive qualities or durability under close scrutiny. This can lead to disappointment for customers expecting longevity and sparkling brilliance from their 3D printing project. As the head of a leading jewelry design house once said: "Our clients expect magic in their jewelry; thus, materials must sing with beauty and resilience." Such reflections underscore the ongoing quest for suitable materials in the niche of 3D printed jewelry.
Samantha Radcliff, a jewelry maker and industry expert, noted, "While 3D printing allows for incredible design freedom, the authenticity encompassing timeless metals and stones signifies the soul of creation."
Additionally, the technology's progression has encountered the hurdle of blending metals with polymers or other compounds to create unique hybrids. Though researchers are steadily working on metal-matrix composites, this remains a burgeoning field with more promise than current application. Consequently, the dream of printing a multi-material intricate piece remains largely conceptual, sparking conversations about future innovations that could transform jewelry making forever.
For now, artisans and designers often employ a combination of 3D printing and traditional crafting to achieve the desired effect. They might print a mold using plastic or wax and then cast the final piece in metal. This hybrid approach is helping to bridge the gap between modern technology and age-old artistry, allowing creators to push the boundaries while adhering to the sometimes stubborn reality of material limitations in 3D printing.
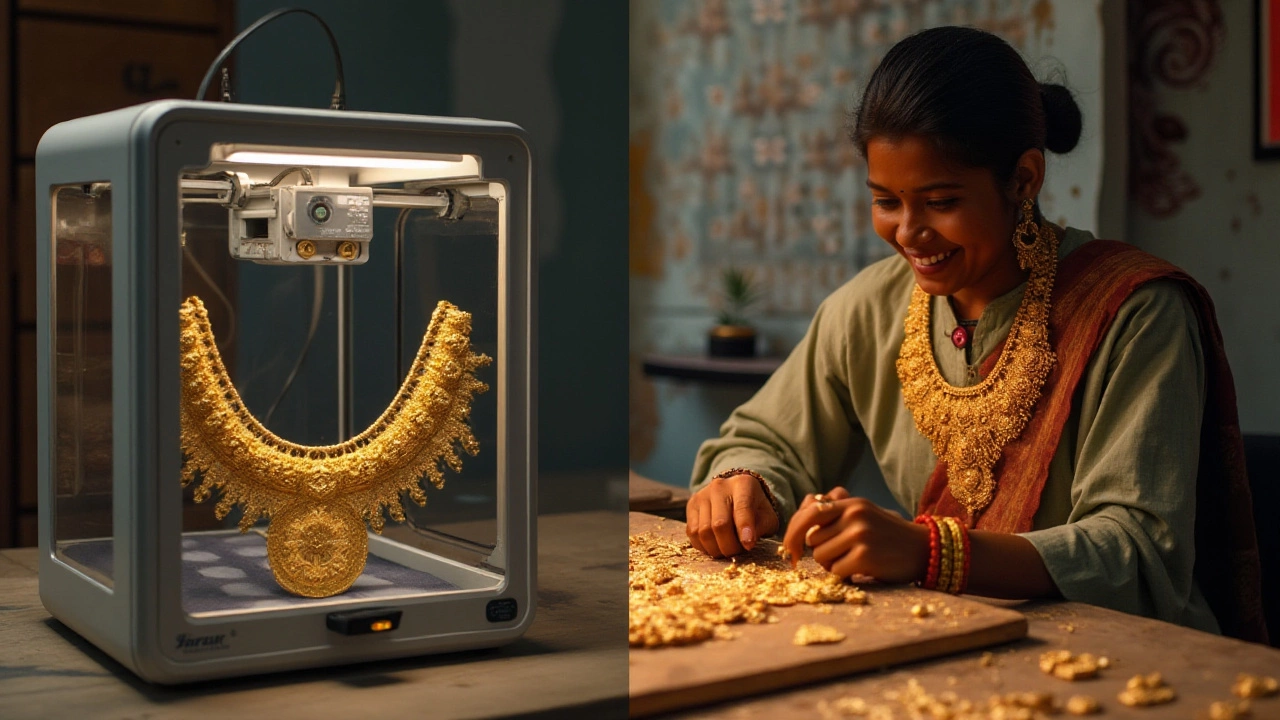
Complex Geometries and Details
Exploring the intricate world of jewelry making, one quickly learns that while 3D printers are marvels of modern technology, they are not without their limits. Crafting heavily detailed jewelry pieces often means transcending what these machines can do. The issue arises primarily due to geometric complexity. Consider, for example, the challenge of creating a delicate lace pattern, a task that requires fineness beyond the reach of a typical printer's resolution. Such designs often come with thin walls or tiny interlacing structures that simply cannot be supported or adequately defined by the machine. The struggle is not just about printing the piece but ensuring it retains its integrity, offering both aesthetics and usability.
Another aspect to consider is the precision needed for certain fit-like qualities in jewelry making. When designing a piece that requires specific fittings such as clasps or prong settings, minute discrepancies could lead to functional failure or a subpar finish. Interestingly, some jewelers prefer to combine both traditional crafting methods with modern technology to overcome these challenges.
As noted by renowned jeweler Jane Collins, "The art of combining computer-generated models with artisan skills allows us to push boundaries while maintaining the artistry that defines each piece."The essence lies in knowing when to let technology take the lead and when to invite the human touch.
Notably, certain 3D printer limitations stem from the inability to utilize specific materials which could address these geometric issues. Even slightly complex textures and patterns can paradoxically make the structure more susceptible to breaking. This is a particular concern when working with materials that have not been designed with additional reinforcing properties. It’s here that laser precision and the chemical bonding available in traditional crafting can save the day, ensuring the piece not only looks stunning but also stands the test of time.
Material science suggests that the layers in a 3D printing process inherently introduce vulnerability to the structure. Imagine designing a piece that requires the seamless integration of hard, complex layers. The additive nature of 3D printing, where layers are stacked upon one another, often leads to visible lines or potential weak spots. This is where traditional methods still hold their place, offering a seamless finish owing to the solid continuous piece created by casting methods.
Aspect | Traditional Method | 3D Printing |
---|---|---|
Detail Precision | High | Moderate |
Material Compatibility | Flexible | Restrictive |
Structural Integrity | Solid | Layered |
Ultimately, while 3D printers have opened new realms of possibility, the artistry entailed in crafting complex and intricate jewelry requires combining these innovations with tried-and-tested techniques to foster a balance where technology complements but not supplants the gold standard of human craftsmanship. This synergy is what truly pushes the boundaries of what is possible in jewelry design, ensuring each piece is a testament not only to contemporary innovation but also to the age-old tradition of jewelry artistry.
Durability and Strength Concerns
When it comes to creating pieces with a 3D printer, achieving optimum durability and strength can pose quite the challenge, especially in the field of jewelry making. Although 3D printers showcase impressive capabilities, the materials most commonly used, like PLA or ABS plastics, often lack the robustness expected of traditional metals such as gold or silver. This discrepancy means that 3D printing has yet to completely replace old-fashioned craftsmanship, which ensures structural integrity over time. While these plastics suffices for many applications, elements like tensile strength, resistance to wear, and flexibility remain areas where classic materials outshine their 3D-printed counterparts.
For those venturing into the realm of 3D printed jewelry making, the choice of material significantly impacts the strength and wearability of the final product. Selective laser sintering (SLS), a popular 3D printing technique, utilizes nylon-based powders that can achieve higher strength than traditional plastic filaments. However, this process isn't without its limitations and still doesn't reach the durability offered by metals. The quest for durable, long-lasting 3D printed jewelry has driven research into new composite materials that incorporate metals, improving both strength and aesthetic appeal. Adoption of new alloys blended with stronger plastics show promise, yet there's still a gap to bridge before complete reliability is achieved.
Interestingly, NIST recently reported that 3D printing could intertwine with metal injection to create hybrid pieces combining strength and lightweight properties, but this process requires high precision and expertise.
"Build material dictates the lifespan of a 3D printed product." - Materials Science JournalJewelers often explore complex geometries that stress-test the printer's limits, demanding innovative designs that guarantee sufficient structural strength. Adopting clever solutions like honeycomb structures can distribute stress more evenly across a piece, amping up durability while keeping weight down. However, these also necessitate an understanding of structural engineering principles, posing additional learning curves to budding designers.
While 3D printing remains at the technological forefront, the need to uphold excellence in intricate creations epitomizes the essence of traditional jewelry makers. As we progress, hybrid methods that marry modern techniques with the wisdom of traditional methodologies offer the most fruitful path forward. Ultimately, the potential lies in continuously evolving materials science, enabling new applications and expanding the possibilities of what can be achieved with 3D printing in jewelry. Until then, traditional metalwork and other conventional craftsmanship approaches will continue to play a pivotal role in ensuring quality and durability surpass the fleeting advances of the printing world.
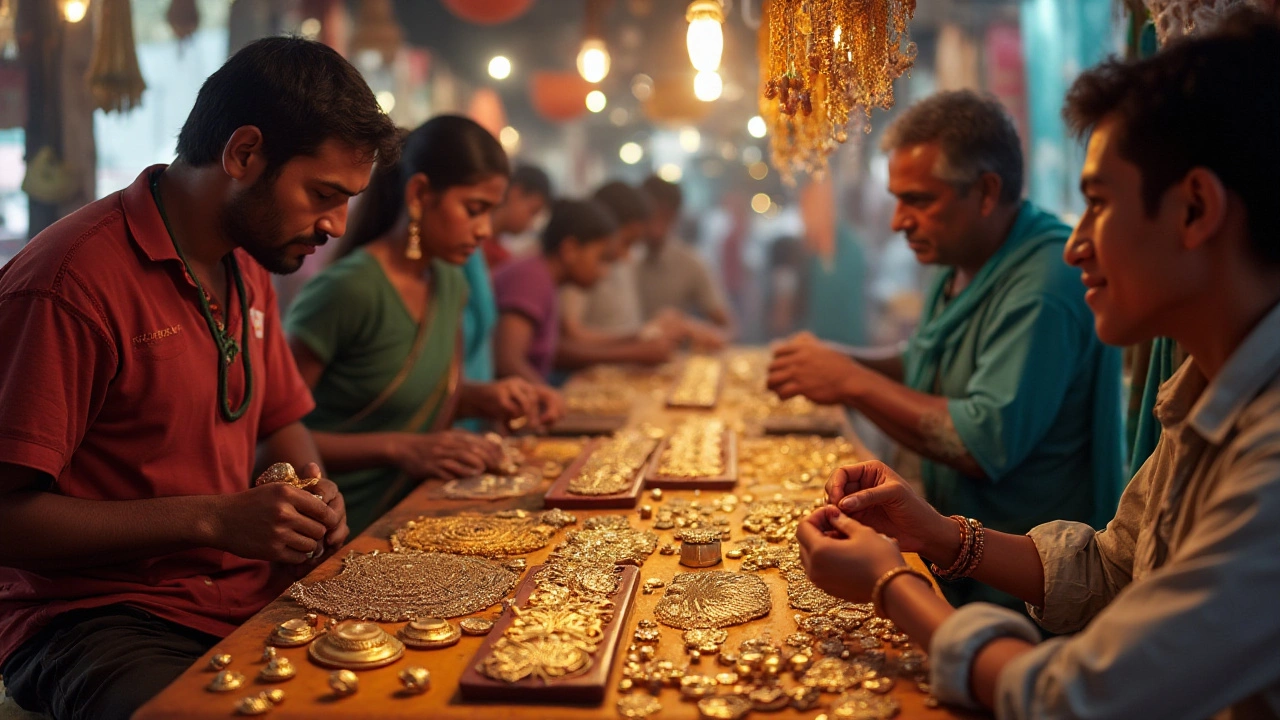
The Role of Traditional Craftsmanship
In the bustling arena of jewelry making, where technology and artistry meet in dazzling display, the whispers of past traditions continue to echo. While 3D printing has paved an extraordinary path for innovation, undeniably, there's a reverence and resilience to the art that thrives beyond the grasp of machinery. The allure of handmade jeweler pieces carries a certain mystical quality, an aura individualized by skilled artisans that machines, as clever as they are, find hard to replicate. Distinctive textures, the warmth of a craftsman’s fingerprints, and the subtle imperfections that characterize hand-forged pieces create a profound connection between the creator and the wearer.
Traditional craftsmanship excels where 3D printers falter. Take, for instance, the notorious difficulty of effectively replicating the gleaming splendor of pure gold in its unadulterated form. When heated and handled by human touch, a piece of jewelry comes alive in a way that automated layers of fused filament can hardly emulate. Custom hand-engraving and the swirling dance of chasing and repousse techniques offer dimensionality and flair that defy the current strengths of modern printing.
The eclectic process of using age-old techniques provides room for real-time manipulation and good old trial and error. In the heart of workshops, artisans find themselves holding raw materials that refuse to bend to silicon's whimsy – like certain gemstones that can fracture or discolor when subjected to even the finest of industrial processes. Indeed, the richness of precious metals can involve the yielding use of rolling mills and stamping presses preconceived with millennia of artisans’ instincts at their base.
A riveting analysis by the Jewelry Institute stated,
"There is a symbiotic relationship between a craftsman's soul and the metal he marries – a dialogue that no machine, however advanced, has managed to emulate with same intimacy."Such sentiments remind one of the irreplaceable value of human touch. It is not merely the outcome that matters, but the journey from a mere sheet of metal or stone to becoming an art of adornment, carrying stories of creation within its veins.
Future Prospects for 3D Printing
As the dust settles on the early advances in 3D printing, the horizon is dotted with exciting potentials that promise to transcend the current limitations—especially in the fascinating realm of jewelry making. The trajectory of technological growth hints at several ways these seemingly impossible hurdles might be overcome. One of the emerging areas is the improvement in 3D printer limitations. Researchers are tirelessly working on expanding the variety of printable materials, inching closer to incorporating exotic metals and precious stones that are often hard to replicate with current technology.
Another avenue showing promise is the refinement of complex geometrical capabilities. Future printers might harness enhanced algorithms and synthetic intelligence to effortlessly navigate intricately detailed designs at microscopic precision. Improvements in printer hardware will play a key role, leading to machines that can handle finer, more detailed work, which is impossible currently. These developments could allow designers to stretch their creativity beyond existing boundaries, opening newer avenues for expression and functionality. During a recent innovation conference, a lead researcher stated,
"The future of 3D printing in jewelry design looks bright, with possibilities we haven't even dreamed of yet."
Looking at durability and strength concerns, manufacturers are continuously innovating in areas like material chemistry and synthesis methods. Imagine printable composite materials designed to mimic the resilience of metals or the organic allure of gemstones. These would be blended at a molecular level, removing current tensile and compressive weaknesses. Such advancements await us right around the corner, with experimental findings paving the path to integrating these futuristic materials with unparalleled strength. Moreover, the inter-disciplinary collaboration among material scientists, engineers, and artists can accelerate breakthroughs.
Then there's the groundbreaking concept of bio-printing for jewelry. Inspired by biology and the ways organic materials self-construct, this approach aims to develop sustainable, eco-friendly designs through a process mimicking nature itself. Not only could this create biodegradable or programmable jewelry designs, but it might also close the gap between traditional craftsmanship and modern technological advancement.
Another dynamic prospect lies in hybridizing 3D printing methods with traditional techniques to strike the quintessential balance where both can co-exist. Workshops and educational hubs worldwide are now focused on intertwining artisanal skills with cutting-edge technologies. Imagine a world where the mastery of human hands is celebrated alongside the precision of machines; the two working in harmony to produce unparalleled creations. The future might not replace artisans but instead enrich their palettes with new colors to paint with.
To sum up without hitting clichés, while the road ahead for 3D printing in jewelry isn't entirely obstacle-free, the thirst for innovation assures it’s filled with entering opportunities. Both challenges and triumphs are steering us towards a future where 3D printing continuously reshapes what's considered possible in the artistry of jewelry creation. And maybe, just maybe, the boundaries of ‘unprintable’ will be redefined not simply by what can be achieved technically but by the shared vision and determination of those who dare to push beyond.