Picture this: You’re wearing a one-of-a-kind ring, and when someone asks where you got it, you say, “I made it at home.” Most people still think jewelry design needs fancy workshops and years of training. Not anymore. With a half-decent 3D printer, you can design and make customized pieces without even putting on pants. It’s not just about flashy tech, either. Artists are selling 3D printed jewelry on Etsy, indie designers are skipping the middleman, and even big brands like Boucheron have used 3D printing to prototype high-end items. Is it magic? Not quite. But trust me, it’s close.
What Does 3D Printed Jewelry Actually Look Like?
Forget the image of clunky plastic trinkets. Modern 3D printed jewelry can be finely detailed, glossy, and just as durable as store-bought pieces. You can print in plastic if that’s your vibe, but the real stars are metal and resin prints. Designs that would be impossible—or super expensive—to carve by hand are now doable with a mouse click. We’re not just talking about simple bands, either. Imagine interlocking geometric shapes, name pendants in your handwriting, or crazy filigree you couldn’t do with a saw blade. There’s this piece by Nervous System—an MIT-founded studio—that uses algorithms to create intricate, organic shapes, all printed in nylon or precious metals. People are blown away that something this artistic came out of a machine.
Materials can make or break the project. PLA or ABS plastic is fine for practice runs and playful stuff, but for something you’ll actually wear, resin is popular for its smooth finish and detail. For metals, things get wild: you can print in brass, bronze, silver, or even gold using a castable resin process and lost-wax casting, similar to the centuries-old method, but way more precise. Some folks print the prototype at home, then send it off to a service like Shapeways or Sculpteo for metal casting. The techiest printers use direct metal laser sintering (DMLS), which fuses metal powder into solid jewelry—seriously next-level, but starts at several thousand dollars.
Another cool fact: jewelers can combine old and new skills. 3D print the base, then hand-set stones or add traditional accents. It’s the ultimate blend of tech and craftsmanship. Some custom wedding rings, with those delicate micro-pave stones, started their journey as a humble 3D model on someone’s laptop.
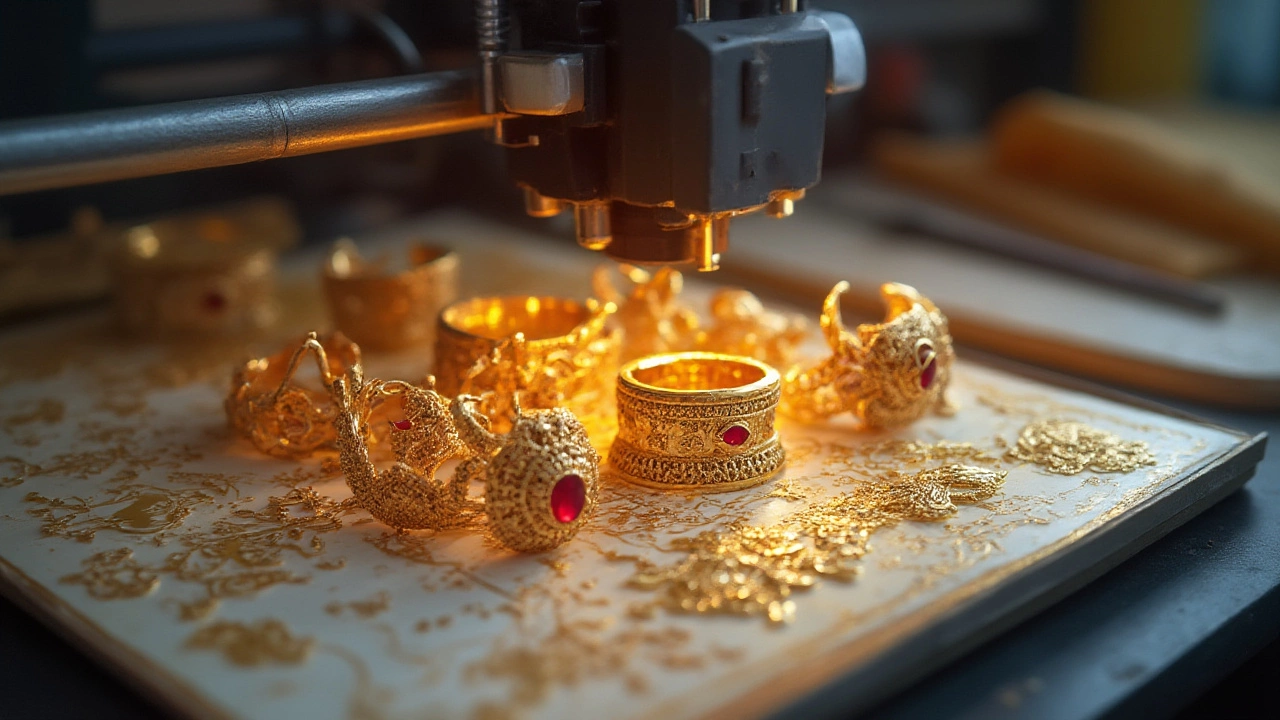
How Does the Process Work? A Simple Step-by-Step Breakdown
So, you want to turn a digital dream into something you can slip on your finger. The process feels a bit like magic, but it’s pretty logical:
- Designing the Model: Everything starts on your computer. Free programs like Tinkercad or Blender can work for beginners, while Rhino or Fusion 360 are pro favorites. If you’re new, start with stacked shapes: rings, charms, cufflinks, or earrings come together from basics like circles and rectangles. People who know CAD crank out wild latticework, custom script, even tiny animal figurines as rings or pendants.
- Exporting the File: When your piece is ready, export it as an STL or OBJ file—these are standard for 3D printing. Double-check for issues like overlapping walls or holes using a repair tool (Netfabb and Meshmixer do the job).
- Choosing the Material: For fast, affordable prints, plastic or resin is your go-to. For full-metal, castable resin is printed, encased in plaster, burned out, and replaced with molten metal in a foundry—yep, like the old days but more precise.
- Printing: Your home FDM (fused deposition modeling) printer will handle PLA or ABS, making chunky practice pieces great for testing if your size is right. For delicate detail, resin (SLA/DLP) printers like the Anycubic Photon can handle tiny earring posts, filigree, and sharp text. If you want gold or silver, most likely you’ll send your file to a pro shop for lost-wax casting.
- Post-Processing: Remove supports, sand rough bits, then polish to a shine. Metal pieces come out of casting rough and need tumbling and buffing for a pro finish. Some jewelry makers also plate base metal prints in gold or rhodium for that deluxe feel.
One cool tip: If you’re struggling with sizing, print a plastic version first. It’s cheap, fast, and saves you the pain of a too-small (or comically large) metal piece later.
Still worried it’s only for tech nerds? Plenty of artists and crafters learned by watching YouTube, experimenting, and sharing failures on forums so you don’t have to. There are beginner kits from companies like CraftCloud that bundle printable files, resin, and even starter tools in one box.
Curious what’s popular? Here’s a quick table with favorite jewelry types people are printing today, plus tips for each:
Jewelry Type | Best Material | Design Tip | Difficulty Level |
---|---|---|---|
Rings | Resin, Silver, Gold | Print test rings for sizing | Beginner |
Pendants | Bronze, Brass, Nylon | Try hollow shapes for lighter weight | Beginner/Intermediate |
Earrings | Resin, Silver | Make matching mirrored pairs | Intermediate |
Cufflinks | Brass, Steel | Add initials or logos | Intermediate |
Bangles | Nylon, Resin | Use flexible materials for comfort | Advanced |
There’s no gatekeeping here. Whether you want to copy vintage art deco or invent your own cyberpunk aesthetic, you’re in control.
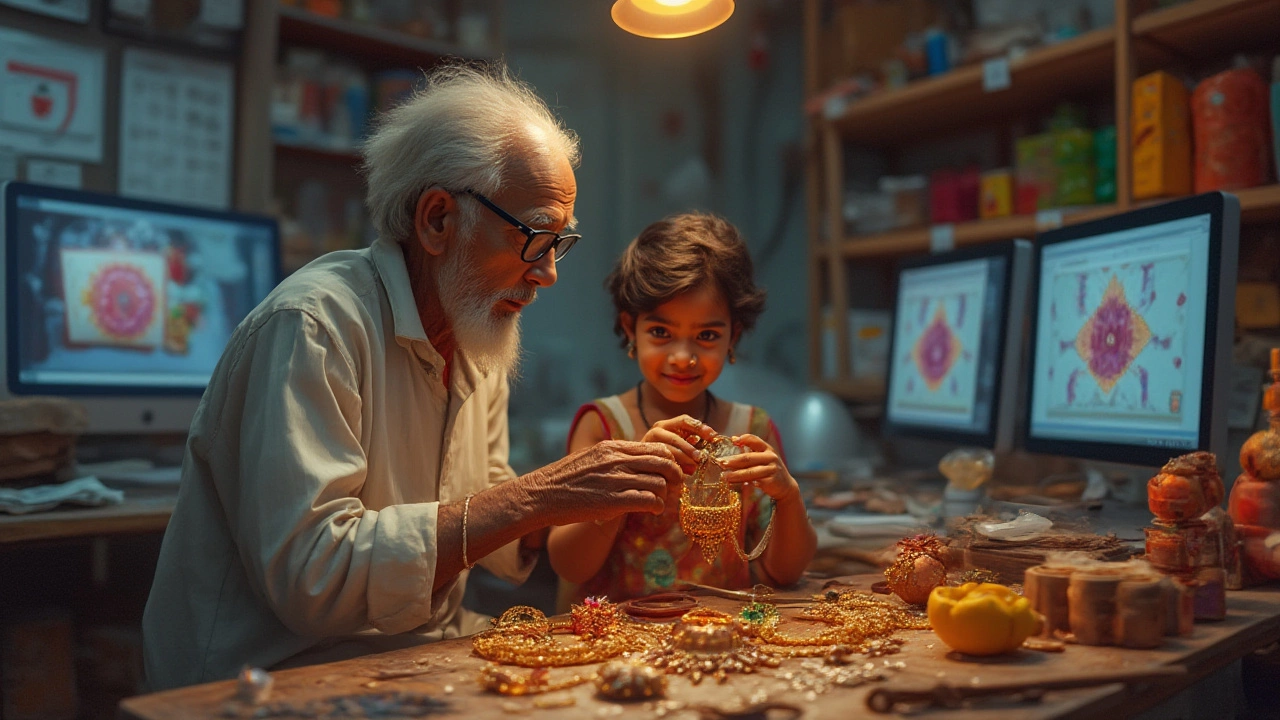
Is It Worth It? Costs, Creativity, and Selling Your 3D Printed Jewelry
Let’s talk bottom line: can you actually save money—or make money—by making jewelry on a 3D printer?
For hobbyists, the start-up isn’t wild. A decent SLA resin printer like the Elegoo Mars sells for under $250. A few bottles of resin ($35 a pop), basic tools (sandpaper, files, cutters), and you’re set. Casting in precious metals does cost more—usually $30-$80 per item plus metal cost if you use a service. Want to make hundreds of items? The price per piece drops a lot after the initial setup. Here’s a quick look at rough, average costs:
Item | DIY (Plastic/Resin) Cost | Professional Metal Casting Cost |
---|---|---|
Simple Ring | $1-2 | $60-120 |
Pendant | $2-3 | $80-150 |
Earrings (pair) | $3-5 | $100-180 |
The real value comes from freedom. You can churn out 20 test designs, iterate shapes, change text, or mash up patterns before ever touching metal. If you want to go pro, platforms like Etsy or Shopify love unique, customizable stuff. Think engraved name rings, birthstone pendants, or geometric ear climbers. Some sellers report that made-to-order 3D printed jewelry nets better margins because they’re not stuck with deadstock.
It’s also a powerful outlet for creativity. Traditional jewelers sometimes spend weeks hand-carving wax molds. With a 3D model, you can tweak, scale, and share digitally—no wasted material if you don’t love the fit or finish. Some specialists use 3D scanning to replicate antique jewelry or to fit a custom piece perfectly to an ear or finger. Even better, many accessible 3D printers now offer micron-level resolution, so details are crisp enough for heirlooms. If you ever wanted to bring wild anime or fantasy accessories into real life, here’s your ticket.
Watch for pitfalls: cheap printers create chunky, brittle results, and low-end resins or metals can irritate sensitive skin (always check for skin-safe materials). And yes, there’s a learning curve—the first few prints might look like toddler art, but the road from “yikes” to “wow” is faster than you’d expect.
The coolest part? The world’s best jewelry designer could be anyone with a little imagination and a 3D printer in their bedroom. If you can dream it, you can build it.